The refrigeration industry has a long history of innovation, and the latest technology is critical to ensuring that the products we buy are of the highest quality. Whether you source parts from overseas suppliers or build your own refrigerator, there are many ways to automate the production process.
Thermoforming
Refrigerator production lines use thermoforming to manufacture enclosures. Thermoforming processes use vacuum, positive air or powered presses to provide the forming force. These forces combine in various permutations and combinations, resulting in a wide range of thermoforming processes. This chapter discusses the main thermoforming processes and their influencing factors.
Thermoforming refrigerator production lines are highly automated and involve a variety of machines. These machines can be configured to meet specific production needs. One is a multi-station vacuum forming machine. It has many advantages, including a high degree of automation, ease of operation and flexibility.
Sub-assembly line
The sub-assembly line of the refrigerator production line is a multi-machine operation that assembles different parts in the refrigerator. This process uses heat and vacuum to create parts of different shapes and sizes. This enables the refrigerator assembly line to meet the customer's process requirements. The process is also efficient and reliable. All parts of the refrigerator are aligned to ensure a smooth operation.
During this process, operators from different operations are assigned to different operations. The two operators assigned to operations 3 and 4 are closer to each other. This change redistributes the work between actions 3 and 4. Additional tools have been added to improve workforce efficiency. So despite the new settings, the average time per operation has not changed. It also reduces the standard deviation.
electrical continuity
An electrical continuity tester is a useful tool for checking the continuity of a refrigerator production line. This tool can be used to measure electrical continuity and locate power sources. Ideally, it should show zero resistance. To test, place the tester's leads on the hot terminals identified by the brass screws. If the tester shows 0 resistance, current flows freely through the wire.
A multimeter with a continuity tester can also be used to test electrical connections and appliances. Its continuity test mode can be used to check switches, fuses, conductors and other components. When a complete path is detected, it emits an audible signal, allowing technicians to focus on their testing procedures. For example, the meter will beep when the resistance of one element is 40 ohms.
Safety
Safety is paramount when assembling your refrigerator. The process involves installing electrical and mechanical components such as controls, heat exchangers, fans and ice machines. Assemblers use various fasteners to hold the components in place. They often use cordless tools to drive screws, and they use DC power tools to drive safety-critical fasteners. The tools are interlocked with the assembly line and automatically stop production if the correct torque is not applied.
Once assembled, the refrigerator undergoes extensive safety testing. For example: refrigerators are transported to the storage line area where electrical continuity and safety tests are performed. They are then tested in a high-temperature, high-humidity environmental chamber to ensure they are safe to use. If the refrigerator fails the safety test, separate it from the functional unit and retest it.
flexibility
The refrigerator line is designed for flexibility. The machine has an outer case with a shoulder mount. It is equipped with side ports on the side facing the transport platform. The bending frame is mounted on this side of the mounting compartment. The machine is characterized by its ability to handle a variety of shapes, both convex and concave. This flexibility allows manufacturers to produce many different styles of refrigerators, regardless of the structure of the enclosure.
The flexible design is possible thanks to the use of three different technical solutions. First, different parts are made from ABS sheet using a thermoforming operation. Thermoforming machines utilize heat and vacuum to shape and form various parts. Second, the flexibility of a refrigerator production line can be increased by using multiple thermoforming machines. This enables manufacturers to better tune their process outputs to meet customer needs.
Air conditioner production
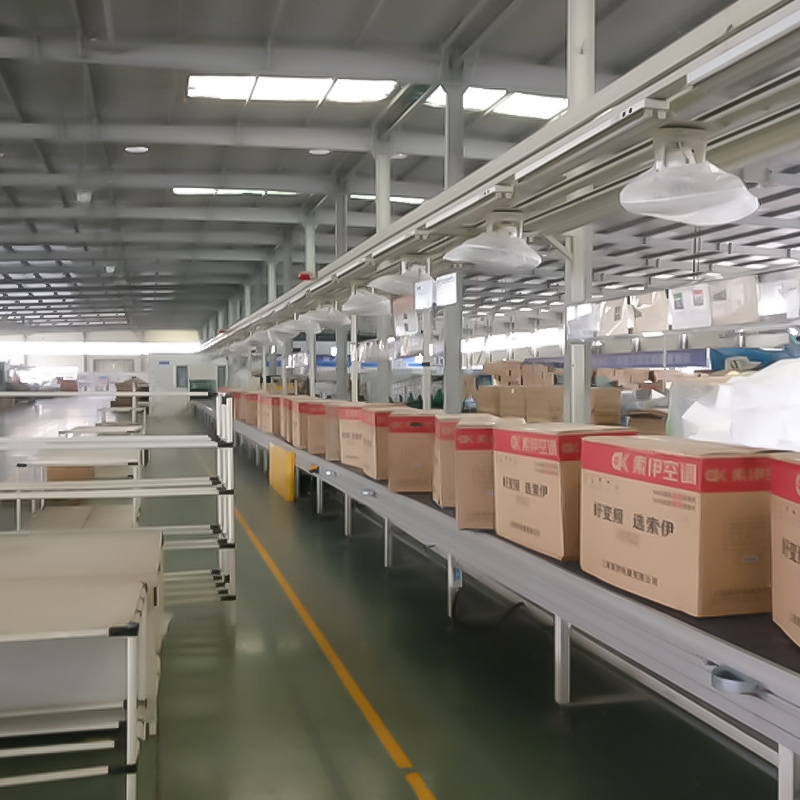
Air conditioner production
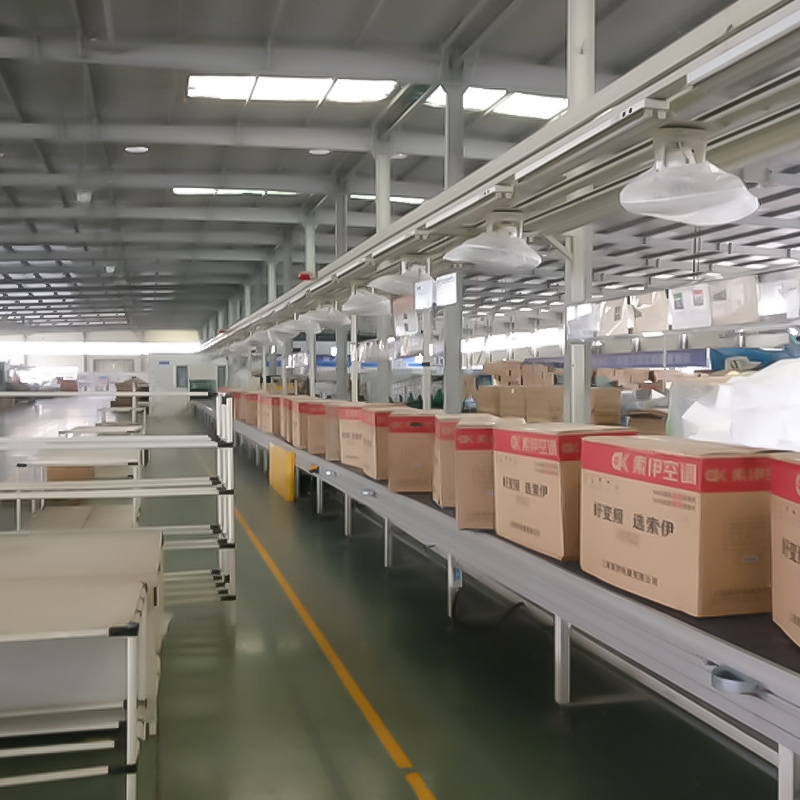
AC solution description:
Main Target Markets
According to air conditioner assembly process flow and plant features, plan the production line layout, propose the appropriate type of conveyance line and realize the streamlined production of the whole production process include the indoor unit, outdoor unit assembly and key components manufacturing, such as pre-assembly, vacuum-pumping, refrigerant charging, safety check, leakage check, performance inspection, packaging and packing, condenser and evaporator production, indoor plastic cover and body injection, outdoor cabinet metal shell. The line can be used for two production modes (SKD and CKD) according to customer budget and part type. The conveyor line can be controlled automatically with PLC with variable speed and stable conveyance.